Comerciais
E se painéis solares no topo do seu camião reduzissem o consumo de combustível?
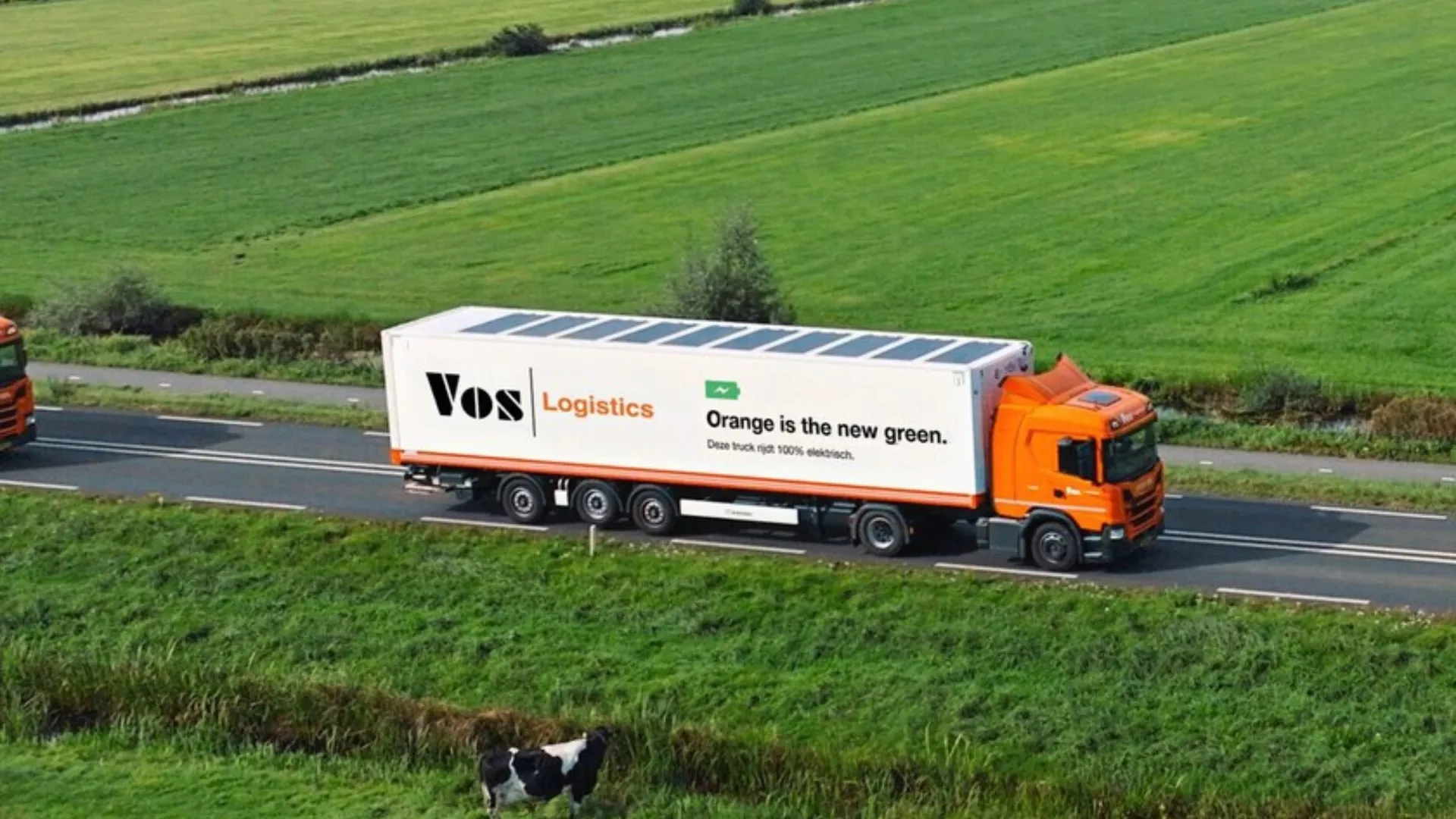
As soluções de mobilidade sustentável estão a crescer com projetos inovadores como o de uma empresa holandesa. A IM Efficiency propõe a instalação de painéis solares no tejadilho dos semirreboques de camiões a gasóleo para reduzir o consumo de combustível, e já provou que funciona.
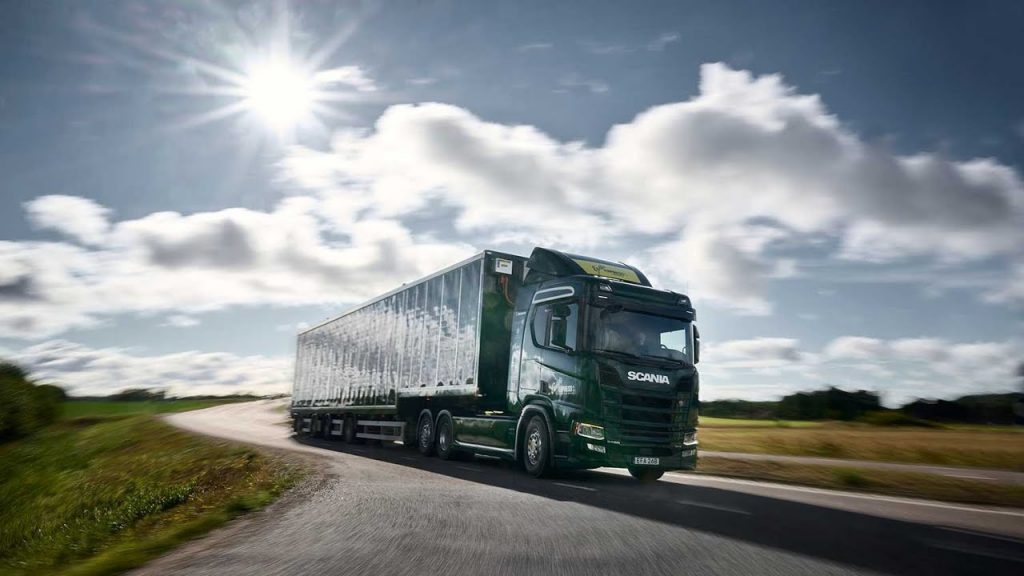
Os condutores teriam de fazer um investimento inicial que, segundo a empresa, seria recuperado ao fim de um ano, após o qual começariam a gerar receitas para as empresas de transportes holandesas. O dispositivo Solar On Top promete gerar 2.000 litros por veículo em camiões e reboques.
O Solar On Top permite reduzir o consumo de gasóleo, por mais contraditório que possa parecer. O alternador é alimentado por energia solar e evita manter o motor em funcionamento para utilizar os sistemas elétricos do veículo.
O Solar On Top pesa apenas 6 kg e os painéis são flexíveis para se adaptarem à superfície de diferentes camiões. Estas células fotovoltaicas oferecem uma potência de pico de 430 watts com uma eficiência de 22%. A bateria de lítio de 4 kWh armazena a energia para fornecer um abastecimento ininterrupto durante a noite ou em dias sem sol.
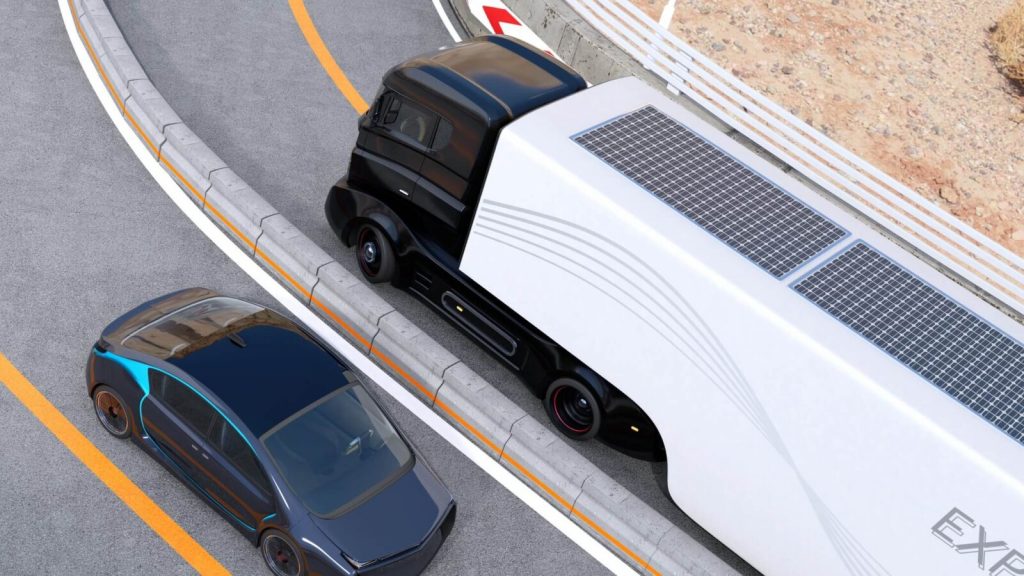
A energia solar recolhida pelo painel pode ser aproveitada para carregar telemóveis e computadores, ar condicionado, iluminação, frigoríficos ou empilhadores elétricos sem depender do motor. A energia solar prolongará a vida útil do motor e da bateria do camião.
Os próprios condutores também beneficiam dos painéis solares. A empresa afirma que o Solar On Top não produz interrupções de energia e permite que os sistemas elétricos do camião sejam utilizados sem o ruído irritante do motor a entrar na cabina.
A IM Efficiency começou a testar esta tecnologia em mais de 100 veículos que já estão a percorrer rotas em toda a Europa. Empresas de logística como a Van Rijnsbergen, a Heisterkamp Transport e a Vos Logistics começaram a fazer encomendas.
Comerciais
Scania lança a solução de carregamento rápido para pesados
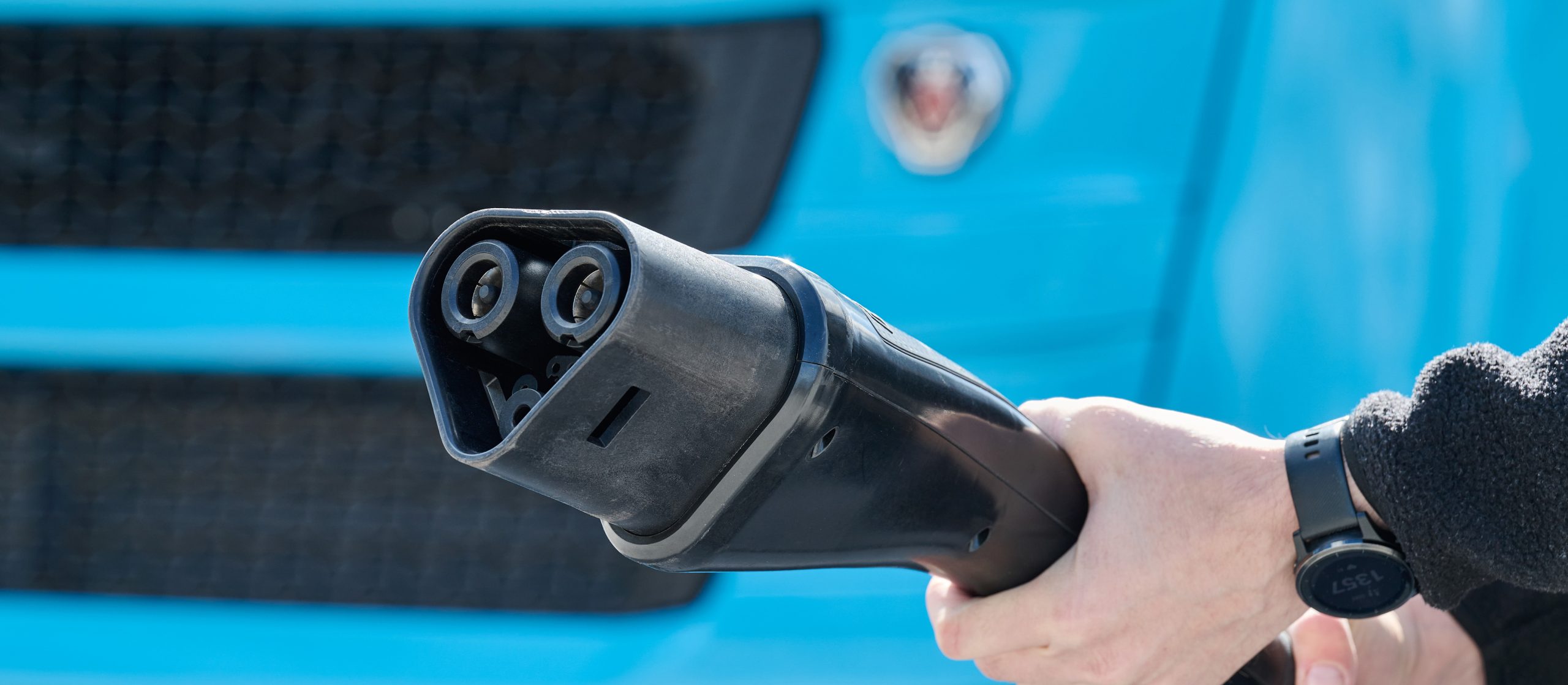
A Scania orgulha-se de anunciar o lançamento do Sistema de Carregamento Megawatt (MCS) para os seus camiões, com disponibilidade comercial a partir do início de 2026.
Prometendo uma capacidade de carregamento muito mais rápida, o MCS marca um passo significativo em direção a um futuro mais sustentável e eficiente para o transporte de veículos pesados. Como norma internacional para camiões elétricos de carregamento rápido, o MCS é especificado para uma corrente máxima de 3000 amperes (o primeiro MCS da Scania fornecerá até 1000 amperes).
Graças a esta tecnologia, um camião pode carregar de 20 a 80 por cento em menos de 30 minutos – integrando-se perfeitamente nos períodos de descanso ou de descanso dos condutores. Este avanço torna o transporte elétrico de mercadorias de longo curso não só prático, mas também rentável.
Com o MCS, os camiões elétricos da Scania podem ser carregados com até 750 kW, o que é cerca de duas vezes mais rápido do que a norma CCS2 atual. Este carregamento de alta capacidade requer soluções inovadoras e seguras, como conectores arrefecidos por líquido no carregador e protocolos de comunicação melhorados, garantindo operações estáveis e previsíveis.
O MCS também aborda outro ponto-chave da atual transição para a eletrificação: o custo do carregamento em termos de preços e do tempo despendido no processo, algo que a TRATON Charging Solutions, o fornecedor de serviços de eMobility dedicado dentro do GRUPO TRATON, que inclui a Scania, considera como um passo crucial.
Os camiões elétricos Scania equipados com MCS estarão disponíveis para encomenda no início de 2026. Simultaneamente, estão em curso esforços consideráveis para construir uma infraestrutura de carregamento robusta em toda a Europa, com corredores MCS planeados ao longo das principais rotas de transporte a partir de 2025.
bento4d situs toto toto togel situs togel situs togel situs toto toto togel toto togel situs toto situs toto bento4d bento4d bento4d bento4d bento4dComerciais
Tour d´Europe reduz 67% as emissões do transporte rodoviário
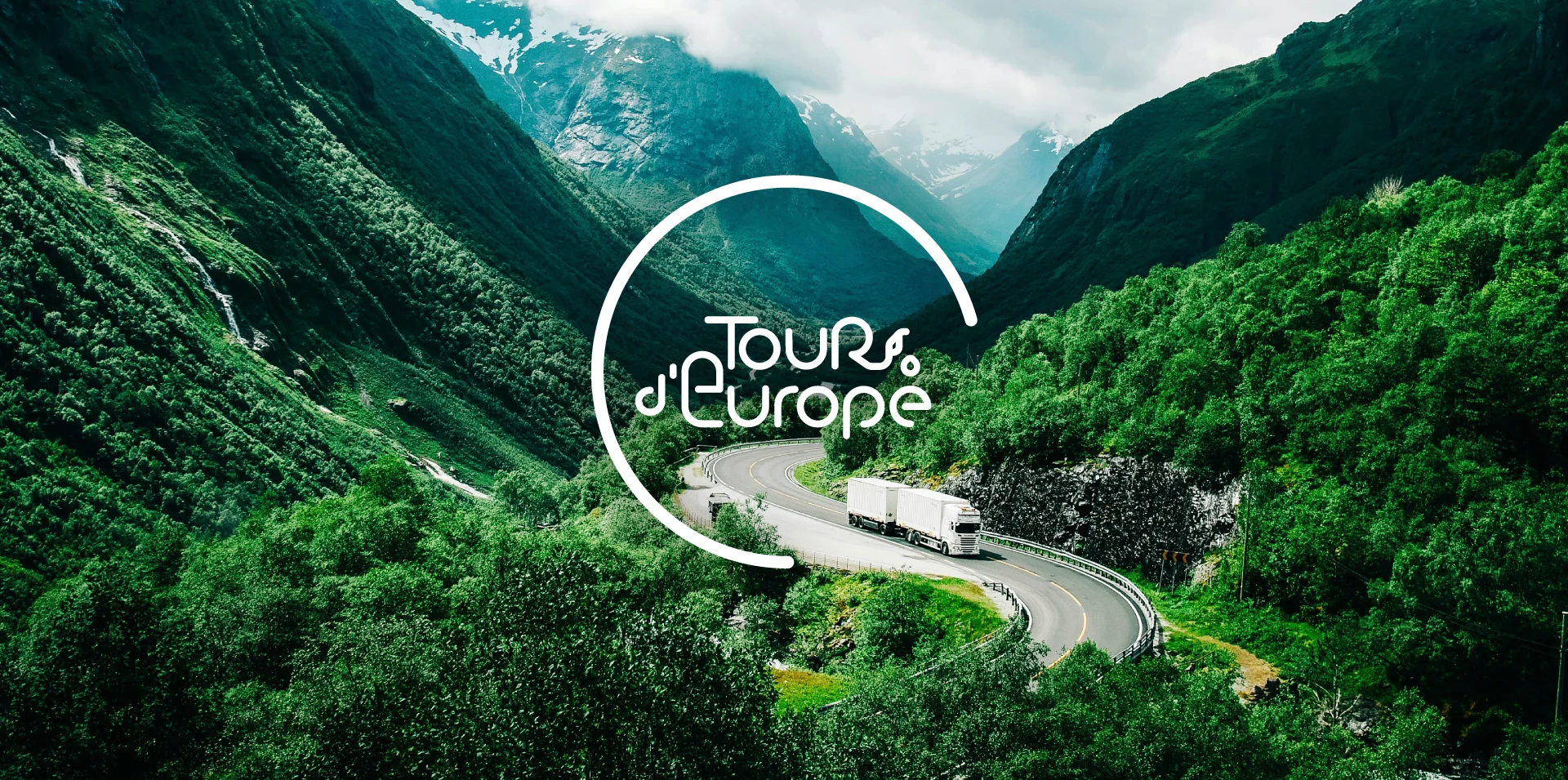
O Tour d’Europe demonstrou com dados que os combustíveis renováveis são uma solução real, eficiente e disponível para a descarbonização do transporte rodoviário.
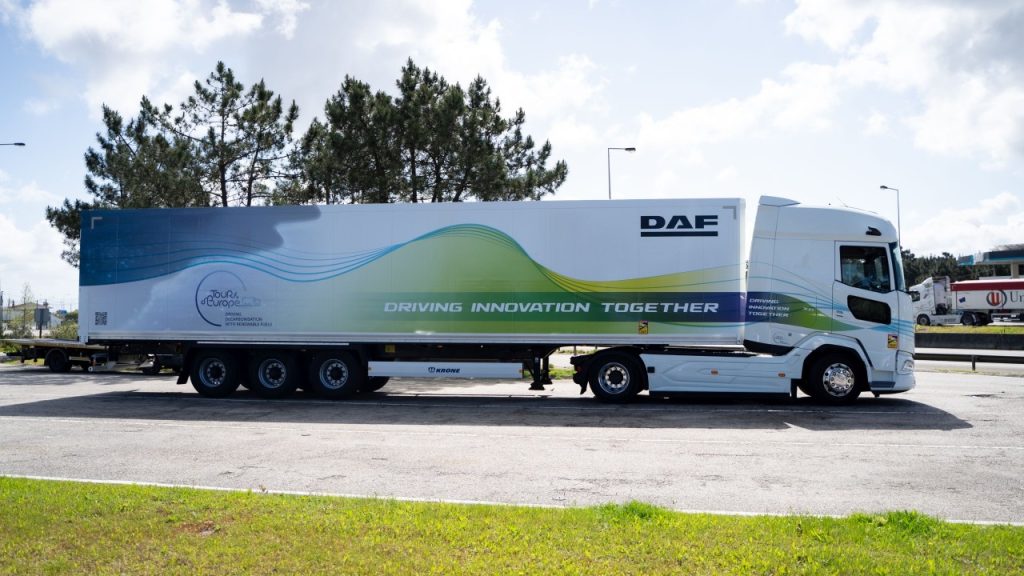
A iniciativa, impulsionada por 26 empresas e associações europeias, conseguiu uma redução de 67% nas emissões de gases de efeito estufa (GEI) em comparação com o uso de combustíveis fósseis, de acordo com uma análise conjunta da Universidade Tecnológica de Darmstadt e do Instituto Tecnológico de Karlsruhe.
Durante o Tour, 84% do percurso foi completado por carros e camiões utilizando combustíveis 100% renováveis. Isto permitiu demonstrar a sua eficácia ambiental e a sua compatibilidade com os motores atuais, sem necessidade de modificar veículos ou infraestruturas.
O estudo revela que os biocombustíveis e combustíveis sintéticos renováveis utilizados alcançaram reduções de GEE entre 66,5% e 83,5%, dependendo do tipo de combustível. Estes números são alcançados de forma imediata, o que os torna uma ferramenta fundamental para acelerar a transição energética nos transportes.
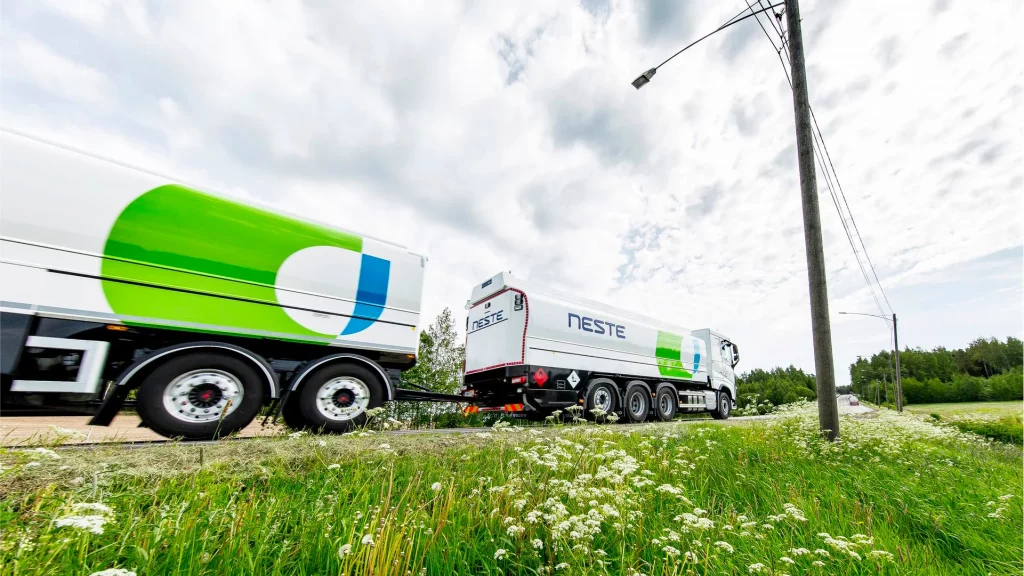
«Cada melhoria nas propriedades do combustível traduz-se numa redução imediata de CO₂», salienta o relatório, que defende a manutenção da neutralidade tecnológica nas políticas climáticas europeias.
A experiência do Tour d’Europe reafirma que os combustíveis renováveis são uma opção viável e já disponível em muitos países da Europa. Eles permitem avançar para um transporte mais limpo sem substituir veículos ou redes logísticas, o que os torna um aliado direto para cumprir as metas climáticas de curto e médio prazo.
situs toto bento4d bento4d bento4d bento4d bento4d toto togel link togel link togel link slot slot resmi bento4d situs toto bento4d situs toto toto togel situs togel situs togel situs toto toto togel toto togel situs toto situs toto bento4d bento4d bento4d bento4d bento4d-
Avaliações Usados2 semanas ago
Smart Fortwo (2014-2020)
-
Notícias1 semana ago
Versões Dual Motor dos Peugeot E-3008 e E-5008 já têm preços
-
Notícias1 semana ago
Range Rover tem um logótipo novo
-
Motos2 semanas ago
Petição contra as inspeções às motos
-
Comerciais2 semanas ago
DAF Trucks apresenta a série XB com carroçarias PACCAR de fábrica
-
Notícias2 semanas ago
O primeiro Bugatti Bolide vai a leilão
-
Notícias4 dias ago
Os preços do novo Audi Q3
-
Manutenção1 semana ago
Como verificar o estado dos travões