Comerciais
Mercedes-Benz Trucks inicia produção em série do eActros 600
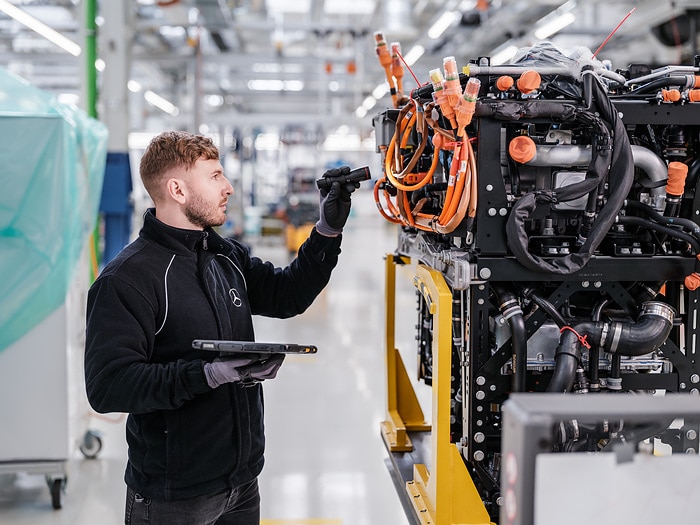
A Mercedes-Benz Trucks vai celebrar o início da produção em série do eActros 600 no final de novembro deste ano na fábrica da Mercedes-Benz em Wörth.
Este modelo foi recentemente reconhecido como o “International Truck of the Year 2025” na IAA Transportation em Hannover. Os primeiros veículos de clientes do eActros 600 serão construídos e registados antes do final de 2024. Em cada um destes camiões, será instalado um componente-chave da fábrica de Mannheim: a chamada caixa frontal.
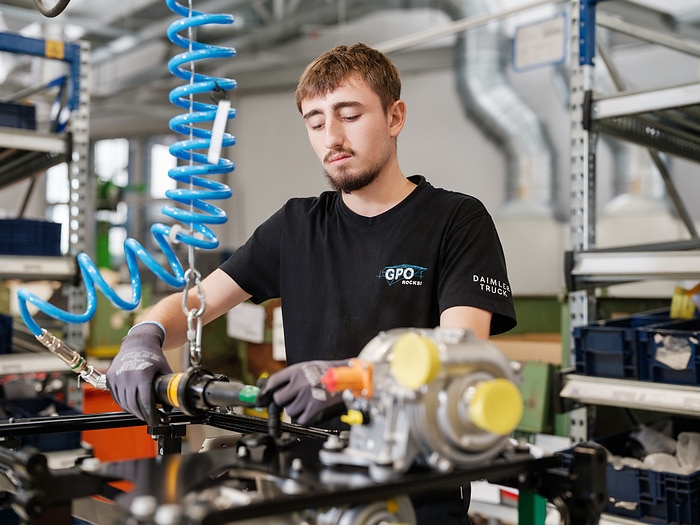
A caixa frontal é um módulo tecnológico complexo que inclui várias unidades de controlo, componentes de alta tensão e um compressor de ar elétrico, ocupando o espaço anteriormente utilizado pelo motor de combustão. Ao contrário do motor diesel, a caixa frontal não tem uma função de propulsão específica, mas aloja numerosos componentes essenciais ao funcionamento do camião. No total, foram incorporadas mais de 1.000 peças individuais. Acomodar este grande número de componentes num espaço pequeno foi um desafio considerável durante o desenvolvimento, que foi resolvido através de uma “estrutura em camadas” que organiza os componentes de baixo para cima.
Andreas Moch, diretor da fábrica em Mannheim, comentou: “A caixa frontal é uma unidade de montagem intensiva para veículos eléctricos. Após uma fase de protótipo bem sucedida, estamos satisfeitos por passar à produção em série. Tanto a preparação do chassis como a instalação de todos os componentes e os testes destas unidades são efectuados na fábrica de Mannheim.”
Moch acrescentou: “A nossa fábrica de Mannheim é o centro de competência para tecnologias de baterias e sistemas de alta tensão na Daimler Truck. Com o início da produção da caixa dianteira, já atingimos o segundo marco deste ano, após a abertura do nosso Centro de Tecnologia de Baterias no verão. Isto mostra que estamos bem posicionados em termos de transformação e que estamos a dar um contributo significativo para a mobilidade sem emissões do futuro.”
Bruno Buschbacher, Presidente do Conselho de Fábrica da fábrica de Mannheim, disse: “Estou muito satisfeito por termos lançado com sucesso o primeiro produto, a caixa dianteira, sob o acordo estabelecido em 2021, e que parte do trem de força para acionamentos alternativos está agora em Mannheim. Este é um passo importante na transformação da nossa histórica fábrica de motores”.
Ao longo de cerca de um ano, foram efetuadas extensas renovações num edifício com mais de 100 anos para criar a linha de produção da caixa frontal. O revestimento do chão de 5.500 m², a ventilação e a iluminação da sala foram renovados, e a estrutura de suporte foi reconstruída. Foi então instalada uma linha de produção moderna com uma área de logística, que oferece um elevado grau de flexibilidade para diferentes quantidades e variantes de produtos.
A linha de montagem da caixa frontal é composta por quatro secções de produção consecutivas. Cada uma destas secções tem várias estações de montagem, com zonas de materiais e estações de pré-montagem nas laterais. Após a conclusão de cada nível, a caixa frontal é submetida a um “controlo de qualidade” para verificar a execução correta do processo de montagem antes de prosseguir.
Para os mecânicos que trabalham na produção da caixa frontal, o lema é: “A montagem continua a ser montagem”, embora de uma forma um pouco diferente dos sistemas de propulsão diesel convencionais. Atualmente, a equipa de produção é composta por 25 funcionários, mas este número poderá aumentar para 170 no futuro. Para preparar os funcionários da fábrica de Mannheim para os desafios da transformação, desde outubro deste ano que recebem formação num novo centro de formação de alta tensão, que oferece um ambiente de aprendizagem prática sobre as mais recentes tecnologias de alta tensão e de baterias.
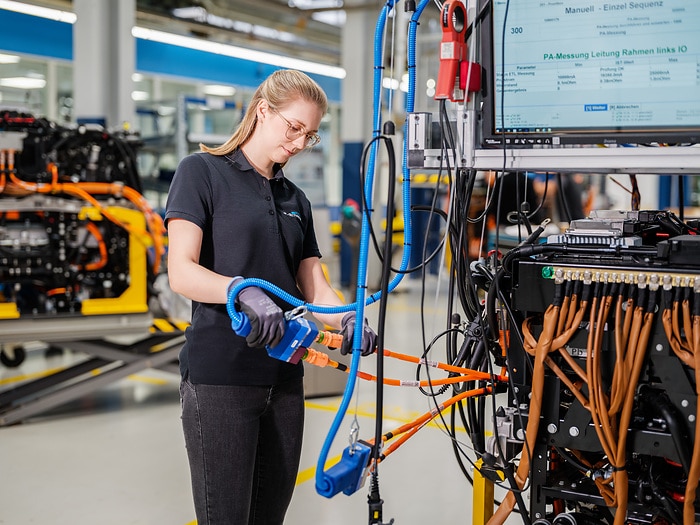
As fábricas de Gaggenau e Kassel, que fazem parte da rede de produção e tecnologia da Daimler Truck para componentes de acionamento elétrico e sistemas de baterias, também fornecerão componentes-chave para o eActros 600. A fábrica de Gaggenau, um centro de competência para componentes de acionamento elétrico, fabricará componentes de transmissão, como eixos e engrenagens, que serão enviados para a fábrica de Kassel para montagem completa.
O eActros 600, concebido para o transporte de longa distância, teve a sua estreia mundial no final de 2023. Com uma elevada capacidade de bateria de mais de 600 quilowatts-hora e um eixo de tração elétrico particularmente eficiente, este camião elétrico pode atingir uma autonomia de 500 quilómetros sem recarga intermédia em condições práticas. Além disso, o eActros 600 terá a capacidade de percorrer mais de 1.000 quilómetros por dia, facilitada pelas opções de carregamento intermédio durante as pausas do condutor.
Fundada em 1908, a fábrica da Mercedes-Benz em Mannheim produz motores e componentes relacionados para veículos comerciais. Com mais de 4.600 funcionários, é também o centro de competência para tecnologias de baterias e sistemas de alta tensão da Daimler Truck, contribuindo significativamente para a produção em série do seu portfólio electrificado. A fábrica também alberga um centro de formação onde mais de 11.000 jovens concluíram a sua formação ao longo de um século de história.
Comerciais
BYD Trucks já chegou a Espanha. Segue-se Portugal
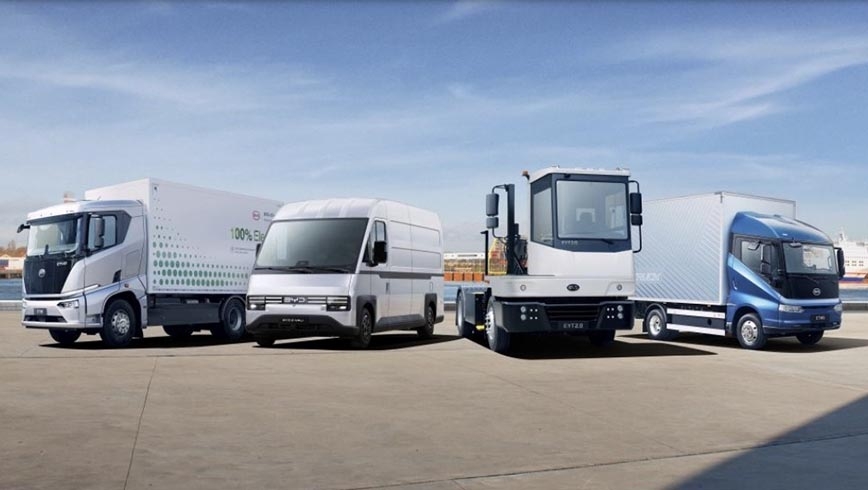
A BYD Trucks, referência mundial em soluções de mobilidade elétrica e pioneira em veículos industriais sustentáveis, anunciou o início oficial das suas operações em Espanha.
Este passo estratégico faz parte do plano de expansão global da marca, que procura liderar a transformação do transporte profissional para um modelo mais eficiente, conectado e livre de emissões.
Após consolidar-se com sucesso noutros mercados europeus, a empresa chega com uma gama completa de veículos comerciais elétricos de última geração, concebidos especificamente para satisfazer as exigências do ambiente urbano e logístico europeu.
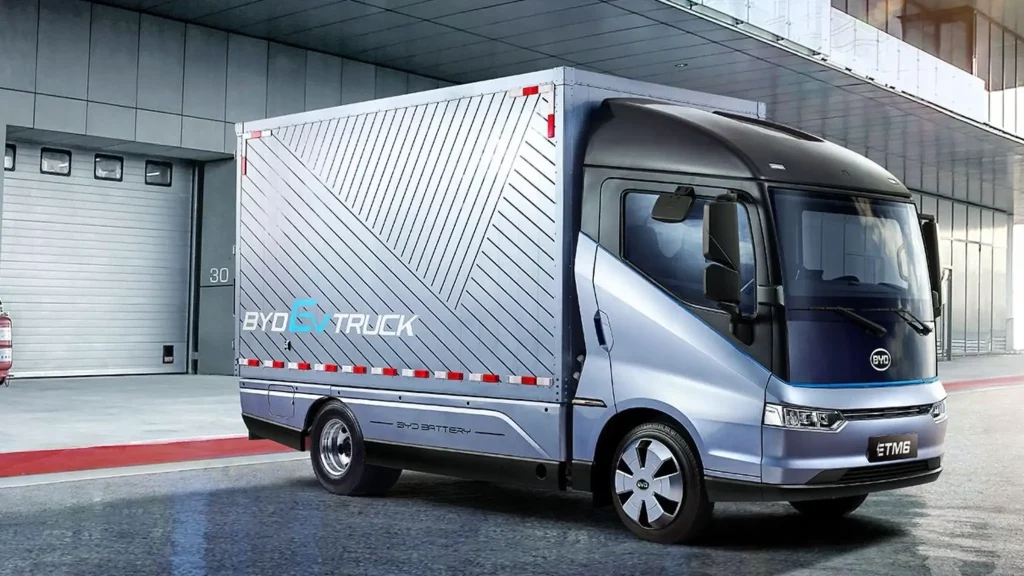
Segundo explica Íñigo Gil de Gómez, Diretor de Vendas para a Península Ibérica: «Sabemos muito bem o que implica promover a mobilidade sustentável. Há anos que nos preparamos para entrar em Espanha e estamos determinados a oferecer aos nossos clientes as melhores ferramentas para a sua transição energética».
A marca destaca que cada modelo foi concebido para reduzir a pegada ambiental, otimizar as operações logísticas e adaptar-se às necessidades atuais do transporte profissional.
Após o sucesso de vários testes na Europa, vários clientes espanhóis preparam-se para testar os veículos da BYD.

As demonstrações incluem: Uma unidade do BYD EVALI eVan; Um trator elétrico para terminais BYD EYT 2.0; Dois camiões BYD ETM6 7.5T, com carroçaria frigorífica e furgão seco
Estes modelos foram desenvolvidos tendo em mente a realidade operacional europeia, combinando autonomia, desempenho e eficiência energética.
Gama elétrica da BYD Trucks disponível em Espanha:
A oferta inicial de camiões e furgões elétricos BYD é composta por quatro soluções 100% zero emissões:
BYD EVALI 4.25T eVan
Furgão de grande capacidade, disponível em versões de carga e cabina dupla.
Volume útil: 17,9 m³
Carga útil: até 1.450 kg
Carregamento rápido: 80% em 30 minutos (188 kW)
✅ Ideal para frotas urbanas com alta rotação
BYD ETM6 7.5T eTruck
Caminhão médio com mais de 1,4 milhões de km operacionais na Europa.
Autonomia: 200 km
Carregamento rápido: 20–100% em 1 hora
Carregamento CA também disponível
✅ Focado na otimização do TCO e uso urbano intensivo
BYD ETH8 18T eTruck
Veículo para transporte urbano de alta tonelagem.
Carga líquida: até 9.950 kg
Autonomia: 250 km
Carregamento de 20% a 100% em 2 horas
✅ Perfeito para logística urbana e recolha de resíduos
BYD EYT 2.0 Trator de terminal
Desenvolvido para operações de alto desempenho e reboque.
Até 85 toneladas GCWR
Duas baterias: 150 e 216,7 kWh
Motores de 130 e 260 kW
Até 16 horas de operação
✅ Solução robusta e silenciosa para portos e centros logísticos
Tecnologia BYD: eficiência, segurança e manutenção otimizada
Todos os modelos BYD estão equipados com baterias LFP (fosfato de ferro e lítio), reconhecidas pela sua alta densidade energética, durabilidade e segurança. Passaram por testes extremos, como o teste de perfuração com prego, um dos mais exigentes do setor.
Além disso, incorporam:
Arquitetura E-axle (eixo motor elétrico)
Controlador 5 em 1 que integra a gestão do motor, distribuição de potência, DC-DC, direção e compressor
Desde a sua fundação em 1995, a BYD consolidou-se como uma empresa de alta tecnologia com mais de 120.000 engenheiros e a maior equipa de I&D do mundo. O seu objetivo: melhorar a qualidade de vida através da inovação e do transporte sustentável.
Comerciais
Amsterdão encomenda 40 DAF totalmente elétricos
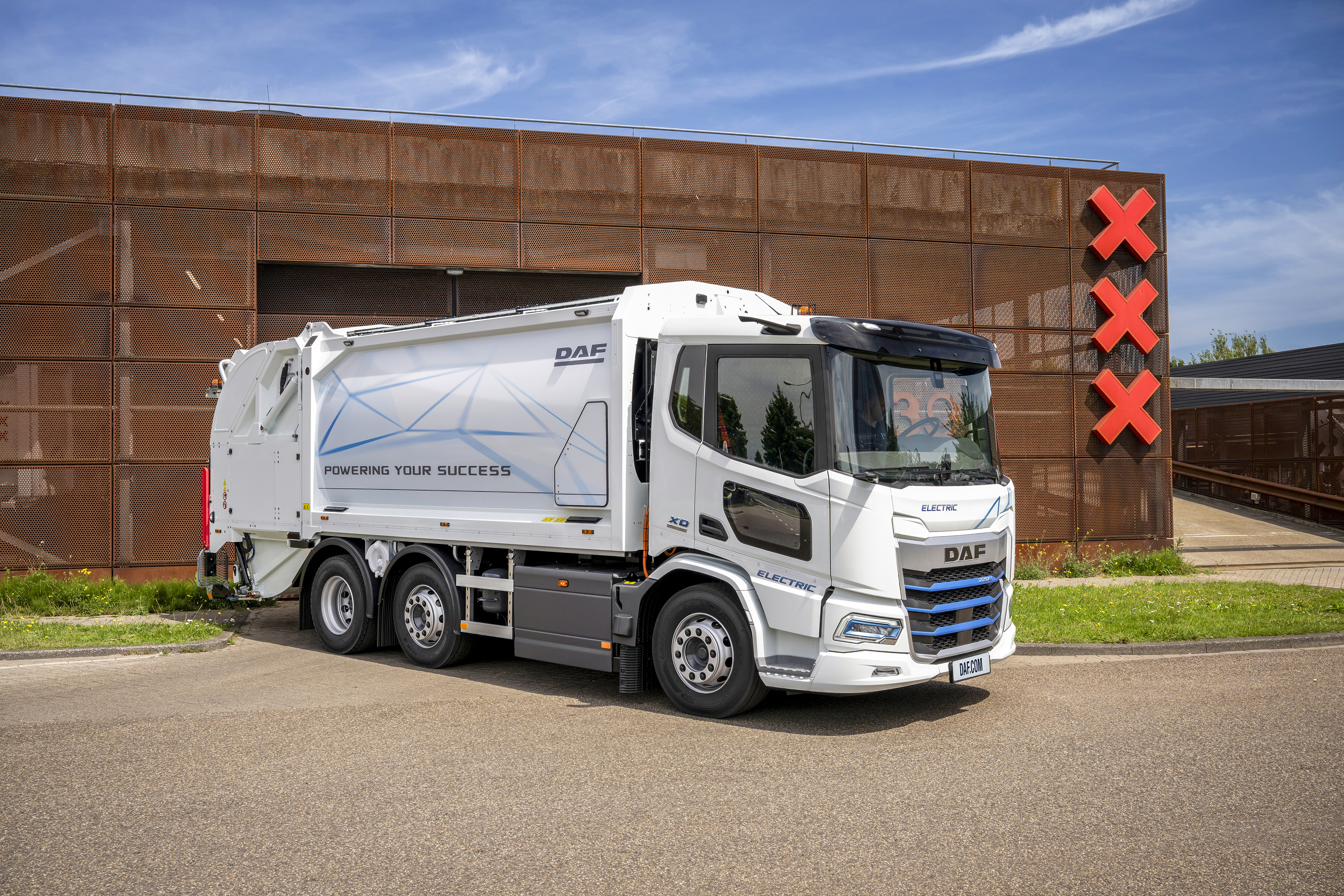
A cidade de Amsterdão está a adquirir 40 camiões elétricos DAF XD para recolha de lixo. Os camiões DAF XD Electric 6×2 FAN serão entregues em 2026 com uma variedade de tipos de carroçaria, cada um projetado para uma aplicação específica.
A encomenda de camiões DAF totalmente elétricos faz parte da ambição de Amsterdão de reduzir ao mínimo as emissões de CO2 e outras. Os veículos serão fornecidos através do concessionário DAF Truckland e VDL-Translift, que cuidará de parte da carroçaria.
Um fator importante na decisão da cidade de Amsterdão de escolher o DAF XD Electric foi sua compatibilidade com a carroçaria. De fábrica, os conjuntos de baterias podem ser montados em várias posições no chassi, de modo que os construtores de superstruturas não precisam realocar componentes elétricos, e há amplo espaço para equipamentos de montagem, como pernas estabilizadoras.
Amsterdão também levou em conta a estratégia da DAF de usar a química da bateria de fosfato de ferro de lítio (LFP). As baterias LFP são livres de cobalto e níquel com uma longa vida útil prevista, tornando-as ideais para utilização em camiões. Podem ser carregados até 100% repetidamente com impacto mínimo no desempenho ou confiabilidade. São também muito estáveis termicamente, garantindo a sua segurança em aplicações como estas.
Os 40 veículos DAF XD Electric para a cidade de Amesterdão serão equipados com diferentes tipos de carroçaria. Estes incluem 13 carregadores traseiros, 10 guindastes e 17 carregadores frontais para recolha de contentores. Com esta nova frota, o município poderá recolher quase todo o tipo de resíduos domésticos isentos de emissões.
Todos os veículos serão equipados com 3 (de um máximo de 5) baterias LFP de 105 kWh cada. Estas fornecem energia ao motor elétrico de 170 kW ou 220 kW do XD Electric. Para alimentar equipamentos, incluindo a carroçaria e as gruas de carga, os veículos serão equipados com uma ePTO de 90 kW.
situs slot situs slot slot gacor link slot bento4d bento4d bento4d-
Notícias2 semanas ago
Setubal Custom Weekend 2025 está quase aí!
-
Comerciais2 semanas ago
Camionista: uma profissão em declínio. O que nos guarda o futuro?
-
Notícias2 semanas ago
Mazda poderá fazer renascer o RX-7
-
Curiosidades2 semanas ago
O arquivo histórico da Lamborghini
-
Motos1 semana ago
Miguel Oliveira fora dos pontos na Áustria
-
Manutenção Motos1 semana ago
Condução defensiva com a sua moto
-
Notícias1 semana ago
Um Renault 4 E-Tech para os bombeiros
-
Comerciais1 semana ago
Nissan eletrifica inaugura estação de carregamento para camiões